Welcome to our official account! Today, we will delve into the workings of industrial syringe pumps and explore how they contribute to various industrial processes. Industrial syringe pumps play a crucial role in accurately delivering fluids in a controlled manner, ensuring efficiency, productivity, and precision. In this article, we will provide an overview of how these pumps work and their applications in different industries.
- Understanding the Basics of Industrial Syringe Pumps:
Industrial syrigne pumps, also known as metering pumps or dosing pumps, are designed to deliver precise amounts of fluids, such as chemicals, additives, or other substances, into a system or process. These pumps are commonly used in industries like chemical manufacturing, water treatment, pharmaceuticals, and food processing, where accurate and controlled dosing is critical.
- Pumping Mechanism:
Industrial Syringe Pumps operate based on various principles, including reciprocating, rotary, and peristaltic mechanisms. Let’s explore the functioning of each type:
a) Reciprocating Pumps:
Reciprocating pumps use a piston or plunger that moves back and forth to displace the fluid. This movement creates a vacuum on the suction side and builds pressure on the discharge side, pushing the fluid forward.
b) Rotary Pumps:
Rotary pumps use rotating mechanisms, such as gears or lobes, to trap and transport the fluid. The fluid is carried around the pump’s casing in cavities created by the rotating components, ensuring a continuous flow.
c) Peristaltic Pumps:
Peristaltic pumps operate by compressing and decompressing a flexible tube using a rotating mechanism. This action creates a moving boundary that propels the fluid through the tube in a pulsating fashion.
- Control and Accuracy:
Industrial Syringe Pumps are equipped with control mechanisms to ensure accuracy and precision in fluid delivery. These mechanisms may include adjustment knobs, feedback sensors, or electronic control systems that allow users to set the desired flow rate or dosage. By adjusting these controls, operators can fine-tune the pump to meet specific process requirements.
- Applications in Different Industries:
The versatility of industrial syringe pumps makes them suitable for a wide range of applications. Here are a few examples:
a) Chemical Manufacturing:
Industrial Syringe Pumpsare used to accurately introduce chemicals for manufacturing processes, such as catalyst dosing, acid neutralization, and pH control.
b) Water Treatment:
Industrial Syringe Pumps play a vital role in water treatment systems by precisely injecting disinfectants, coagulants, and pH adjusters to ensure water quality and safety.
c) Pharmaceuticals:
In pharmaceutical manufacturing, syringe pumps are utilized for metering active ingredients, excipients, and binders during formulation and tablet compression processes.
d) Food and Beverage Processing:
Industrial Syringe Pumps are employed to dose flavorings, preservatives, colorants, and other additives, ensuring precise blending and consistency in food and beverage production.
Conclusion:
Industrial syringe pumps are essential tools in various industries, enabling accurate and controlled fluid delivery. By understanding the different pumping mechanisms and their applications, companies can choose the most suitable pump for their specific needs. The reliable and precise performance of industrial syringe pumps enhances process efficiency, ensures product quality, and optimizes productivity across different industrial sectors.
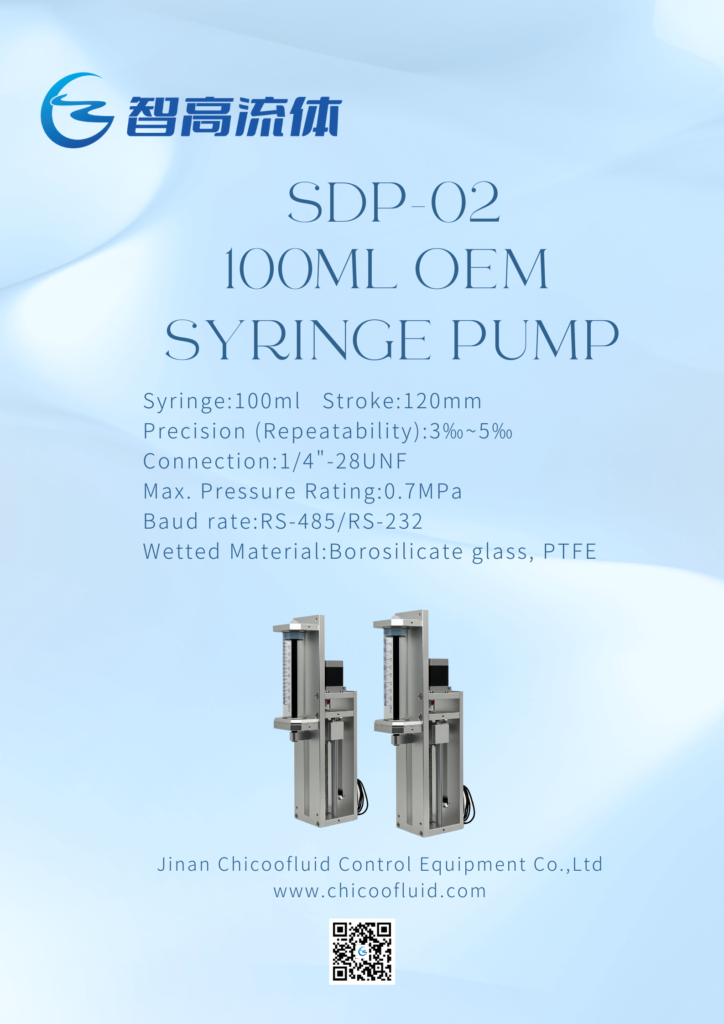